Do you find yourself putting things off on a regular basis? Do you struggle to catch up and stay ahead? If this sounds like you, then CMMS might be exactly what you need and you shouldn't wait.
Why CMMS Implementation Provides Optimum Benefits
When purchasing a Computerized Maintenance Management Systems (CMMS) program, there are many benefits that are expected to be delivered and these benefits include:
- Improved employee productivity resulting in reduced labor costs
- Increased equipment availability due to better planning
- Increased equipment reliability through the identification of repetitive faults
- Improved inventory control, making stock more leveled off
- Improved long-term reduction in maintenance costs
- Improved safety by providing detailed standard job protocol
In most cases, maintenance departments will see clear financial justification as well as the increase in benefits that help the department run more efficiently. Along with better stock control, increased employee productivity, better planning and preventative maintenance, and more – the addition of saving money long-term adds up to substantial advantages by implementation of a this type of program.
How does this work? And how have so many who have successfully gained benefits from a new CMMS achieved that success? These questions are the subject of this paper.
The Six Levers of Change
In the early days of Computerized Management Systems, some people thought that just simply introducing the new technology would be good enough to get everyone on board. Of course the software has the added benefits mentioned, but there is a way to ensure a more successful implementation that fulfills all of the needs and promises, while making optimum use of the technology and what it can do for a Maintenance department.
More recently, it has been recognized that, while it can be a significant enabler of improved Maintenance performance, to achieve the maximum possible benefits from this type of implementation, business processes do have to make a change. The good news is that change is good and allows the company to grow and succeed better through positive changes. So, the Business Process Re-engineering (BPR) approach to Systems Implementation was created, which focuses on both the technology and the business processes involved in a program execution.
While some may debate the BPR approach, it is an approach that is successful in achieving sustainable advantages that are good for the long-term of the business.
Price Waterhouse has found that it is useful to consider effective organizational change as happening along six dimensions, called the 6 levers of change. These are illustrated below.
What this suggests is that one of the best ways to introduce these improvements is to pull all of the levers of change in a coordinated manner. Everything has to be proactive so that the people who are affected by the changes are actually committed to it.
Let’s focus on the tactical levers of change within the realm of only those affected within the maintenance department such as the staff and management.
Maintenance Processes – A Framework for World Class Maintenance
In general terms, the maintenance management process can be considered as having six phases, which you can see in the illustrations below.
This works by putting everything together – plans are implemented, the correct actions are taken, and then the outcome is compared to what was originally being done so that the right action can be taken.
In order for implementation to have the best success, the above steps should be taken – the comparison is important in order to fix any issues that may arise while everything is new to the department and the staff and management is getting used to the changes.
Once the effort is put in, it becomes even more beneficial to everyone – even more so than before.
The specific feedback loops and processes that are required in a successful Maintenance Management process include all of the following.
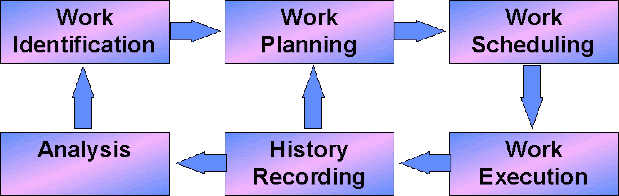
Daily Scheduling and Job Control
This covers such areas as how work is allocated to the workforce, and how expectations are generated regarding a "reasonable" time for job completion. It also includes how daily priorities are set, and decisions made regarding the deferral or cancellation of planned work in order to incorporate daily breakdowns.
This program helps facilitate this process. It provides an easier way to schedule work quickly and efficiently on a daily basis and allows management to allocate work to employees faster and with a way to work within last-minute changes. It also allows management to have a way of analyzing any future job delays and have an option to reduce or eliminate delays and downtime.
Effective Weekly Scheduling Control and Management
This incorporates the development of a Weekly Schedule, but more importantly, also includes control loops that ensure that the Weekly Schedule is realistic and achievable, and also works towards a steady increase in the amount of scheduled work, relative to unscheduled work.
A CMMS program does more than that however. It also allows management to schedule work tasks on specific days so that parts are available when they are needed and preventative maintenance on equipment can be performed without interfering with the work tasks that need doing. It allows the comparison of work requirements of a schedule to the actual amount of labor available for each day, week, or month and lets the maintenance department make the decision of if they need supplemental labor through either contract work or having extra employees come into work – or in some cases, a revamping of the schedule to accommodate these needs.
Basically, it allows you to better analyze data so that it fits your needs with a weekly schedule, work orders, and having enough help to cover all of the work tasks that need completion.
Job Planning Improvement
All maintenance departments on average, plan their work schedule, but some go further by planning the labor requirements, what parts are needed, the cost of the labor being done, and every specific that goes into each work task. An analysis of this type of planning is available in these type of programs and that goes a long way in helping management do more than just schedule a job or work order.
Maintenance Budgeting and Cost Control
It just makes sense that if you are doing maintenance work then you will have costs involved. While every facility will prepare a budget, what some maintenance departments do is prepare their budgets and compare it against the final outcome. Meaning, you have a budget to go by but some departments go above and beyond and compare the final costs against their original budget to see if they were on-track, which gives them even more control over keeping up with profit and loss. A Computerized Maintenance Management Software program allows the ability to run reports that showcase the final outcome, which is imperative to knowing every aspect of where the money is going and how to fix any issues with what is budgeted and what the final cost actually is.
While the management team may set up the initial budget, those at the foremen and staff levels have their part as well which is why a good program will help keep up with costs no matter where the money is going to and it makes it easy to find out exactly where that is.
Maintenance Effectiveness Improvement Processes
There is another process which really separates the most successful maintenance departments from the others. Some focus their attention on maintenance efficiency, which is perfectly fine and good. However, there is another area of this sector which is more effective and that is maintenance effectiveness which includes failure analysis and reliability centered maintenance analysis – among other things. Basically put, one is doing things right and the other is doing the right things.
A Computerized Management System provides valuable information to assist with these analyses. To make educated decisions regarding Equipment Maintenance Strategies and equipment design modifications, there needs to be a record of a few key elements such as:
- The number of failures
- The basic cause of the failures
- What is the cost of the failures
- The production costs associated with those failures – note that these may incorporate more than just downtime costs.
- Any safety or environmental implications associated with those failures.
The key with all of these processes is to start by establishing your control processes and decide on their information requirements. After that has been done, establish the codes, systems, and procedures within the program to provide that information.
Skills and Culture – What Skills are Really Needed?
One of the aspects of a successful implementation is to keep the people aspect in mind. Some staff members may not be as comfortable with some of the lighter aspects of maintenance performance but it is important to remember that skills, as well as culture plays a key role in successful implementation.
What skills are needed for successful implementation?
While it is imperative to focus on the mechanics of CMMS implementation so that users know how to operate the system it is just as important for them to know why they are using it. Once users understand the importance of the data that they are inputting, how it is planned to be used, and why it is being used – there is a better chance that the operator will do things the correct way right from the start. This works even better for those who are using the system to be part of the decision making process.
Read More: Implement Effective Maintenance
By combining these principles along with the implementation, there is more success on getting the most out of the program. Another factor to consider is that maintenance planners who have skills in job planning and those who have leadership and management skills seem to have better success in making the most of your Computerized Management System. Some skills like failure investigation and analysis and/or reliability centered maintenance are also helpful skills but they are not something that not having will hinder the role of the program since it is effective on its own. It is simply that these skills help in all aspects of the maintenance department.
What Organizational Culture leads to successful implementation?
OCI has developed a method of measuring organizational culture along a number of dimensions. These can then be documented in a pictorial form, as shown here. At the highest level, there are three descriptors of cultural style. These are:
- Aggressive/Defensive Styles
- Passive/Defensive Styles, and
- Constructive Styles
Aggressive/Defensive Styles are typically characterized by high levels of competition between individuals and groups. Passive/Defensive Styles are normally characterized by a high level of conformity and adherence to rules and procedures. Constructive styles involve individual and team affiliations, and creative processes.
In a maintenance environment, an appropriate mix between Passive/Defensive Styles and Constructive Styles is a better fit for everyone involved. For a successful implementation, input and analysis of data has to be done correctly. For safety reasons, individualistic behavior is not always the best type of behavior to have but too much conformity can lead to a stagnant maintenance department. It is ideal to have a happy medium between the two types.
To support this desired culture, it is essential to put in the appropriate rewards and punishments. An essential element of implementation is regular audit of compliance with the defined maintenance management procedures, together with an audit of data accuracy and timeliness. This is most effective when these become formal parts of an individual or team's performance appraisal remuneration.
Implementation where the system disciplines are not in place, and people are not rewarded for compliance with the defined procedures cannot excel as well as those who implement both along with the program.
Organization and Structure
Some maintenance departments have made the move to restructure the facility so that the production or operations departments are reported to at a lower level in the organizational hierarchy. This is a trend based on what is called operator maintainers in production departments.
Both of these trends could be explained by an increasing understanding of what Maintenance is all about. The Oxford Dictionary defines "maintain" as "to cause to continue.” If we define equipment maintenance as any activity that is intended to ensure that equipment continues to fulfill the functions expected of it by production, then it is quite clear that many of the activities routinely performed by production personnel (such as routine inspections, equipment cleaning. and housekeeping) are, in fact, maintenance activities that fall under the preventative maintenance umbrella.
The implication is to be able to distinguish between those maintenance activities that you wish to track through the program, and those that you do not. For example, do you consider that time spent by production workers changing AC filters as maintenance? Should you track failures of those filters in exactly the same way as you would any other significant component? The answer should be clearly yes since these are all preventative maintenance duties.
Facilities who do not control such activities are missing out on the full advantages of a Computerized Management System program by Maintenance Care.