There’s no doubt that you remember the time when all maintenance was paper-based. Not the actual tasks, of course, but all the administrative work and information was in countless books, logs, and sticky notes. Even when spreadsheets came to replace them, it was still hard to monitor work orders. Now many companies choose to switch to a CMMS-supported work order management. In one of our previous blogs, we covered various types of maintenance, and today we’ll dive into kinds of work orders and why you do need to differentiate between them.
Basic Types of Work Orders
Preventive maintenance is a vital part of your overall facility maintenance strategy. While on-demand work orders are always unexpected and often urgent, preventive maintenance work orders can be easily planned and scheduled in a CMMS software of your choice. Most often, PM tasks are associated with assets and systems, like HVAC, for example, so it’s great to have an opportunity to set task frequency, time of day, and assignment responsibilities. What’s more, when you know which work order is scheduled for when, you can easily track the inventory and ensure that all the required spare parts are available. Besides, by analyzing routine preventive maintenance schedules, you can minimize your team's downtime and allow them to spend more time focusing on urgent requests.
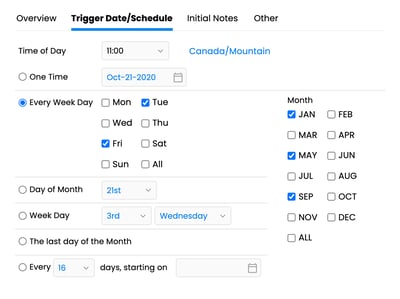
Some work orders are impossible to predict. For example, while predictive maintenance generally extends the lifetime of equipment, a fridge can break down at any time, resulting in extra costs. More than that, not all work orders need to be predicted. Light bulbs, for instance, are pretty cheap and easy to switch, so it doesn’t make sense to include regular bulb checks in your preventive maintenance plan. That’s what emergency work orders are for.
The next type, inspection work orders, often fall under the category of preventive maintenance due to the fixed schedule. However, thinking of inspection work orders as a separate group is just as reasonable because, in this case, you won’t need to filter all PM work orders to create a report for an inspector or to prove that your facility is compliant.
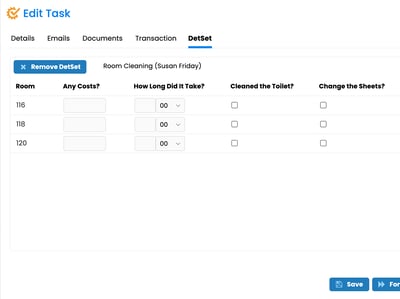
Another special feature of inspection work orders is that they often contain checklists. For example, with Maintenance Care CMMS, you can add checklists or use DetSet (Detailed Set of questions) to make sure that all inspection work orders are standardized and as detailed as they’re supposed to be.
The last type we’d like to cover today is corrective maintenance work orders. In simple terms, when your maintenance technician finds out that something else requires attention while completing another work order, they can create a corrective work order. Of course, they can fix it on the spot and consider it complete, but it’s necessary to keep in mind that work orders are created not only to get the work done. They also serve as a source of critical data about your day-to-day operations. With CMMS, you can investigate the analytics and reports to see the big picture, resulting in more informed decisions.
Integrating Work Order Types into Your Maintenance Strategy
The fact that now you know the functions of different work order types doesn’t mean that from now on, you must always classify all the work orders in your maintenance department. With all this information in mind, it should just be easier for you to assign, track work orders, and go beyond by analyzing and optimizing the operational side of your facility maintenance. A proper CMMS solution is the right tool to use if you want to balance between preventive and emergency maintenance, corrective and inspection work orders. Contact our experts today to find out how Maintenance Care CMMS can help you create a more efficient maintenance department and run it smoothly.