One of the main causes of poor reporting in maintenance management is because the right data never made it in there in the first place.
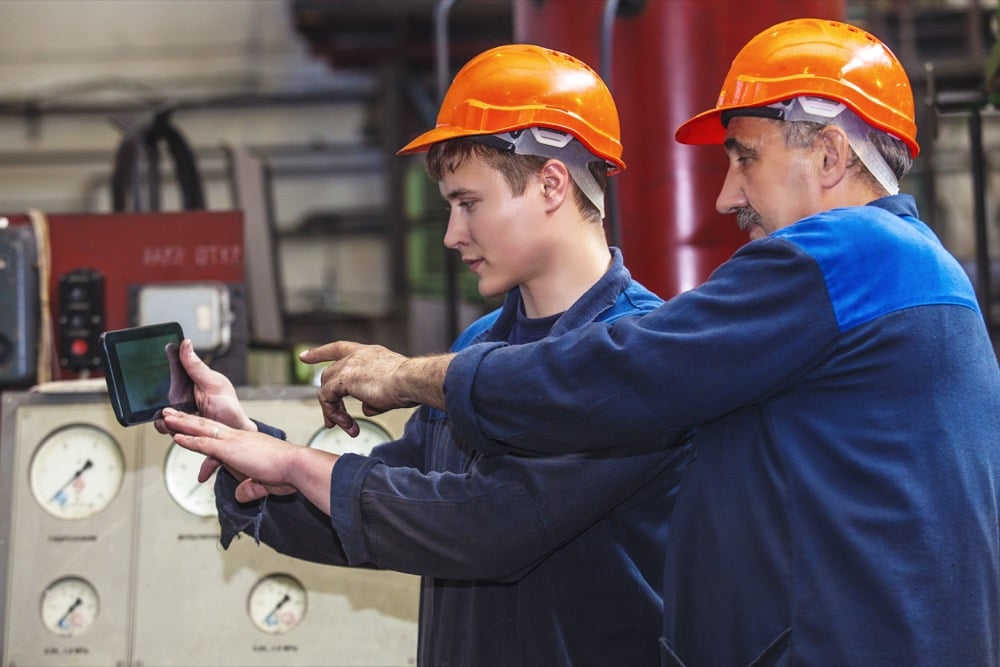
- Paper notes get lost before being recorded in your paper or digital logs
- Maintenance staff forget to enter their findings entirely
- Staff miss recording key points lost between observing the equipment and recording their work – sometimes hours later
- Maintenance tasks get missed entirely
So many things can get in the way of proper maintenance recording. Your staff might service your HVAC, and then get intercepted on the way back by someone else who needs something done. They might have a long list of tasks to complete and won't be back for hours. Or when your maintenance staff feel constantly busy, it's grows easier for them to consider the logs as a lower priority than the actual work.
Solve This Maintenance Reporting Problem By Logging Reports At the Point of Work
You've already got a secret weapon! Whether company-provided or personal, almost everyone already has a smart phone that they're at least using for some work purposes.
So, let's say your paper-based or spreadsheet-based logging were replaced with a digital database that you can access anywhere, just like any website.
Wouldn't it be great if you and your staff could simply record this vital information even as they're doing their work?
You'll cut down on mistakes and missed logs because you've eliminated that time period between the work and the log. If you need to record the state of some piece of equipment, or a reading on a meter, you can do it right there as you're still looking at it.
How Do You Improve Your Maintenance Reporting? CMMS
CMMS, or Computerized Maintenance Management Software, facilitates this. It centralizes all your maintenance task information in a cloud-based platform that you can access from anywhere with an internet connection.
Like the smart phone you and your maintenance staff already carry everywhere with them.
With CMMS, employees get notifications instantly via the app on their mobile device. These notifications promote better maintenance work firstly by allowing you to schedule your maintenance in advance, including all details about the task to be done — and second, it can clearly set out and collect the information you need for your maintenance reporting.
And with that more accurate, reliable reporting, you can now do everything from estimate the value of your assets, predict replacement timelines, and identify costly problems before they happen.
Want to give all this a whirl? Try Maintenance Care. Book a demo today, and our experienced staff can guide you through exactly how you can apply all this to your workplace.